Contents in this Page
Introduction
In 1995 Ford Motor Company undertook a company-wide re-engineering initiative which Ford termed Ford 2000. Ford implemented lean manufacturing. The company called it Ford Production System (FPS) which aimed at making a lean, flexible and disciplined production system which is based on some production principles. This paper has analysed lean manufacturing in production system.
Ford has implemented some production principles that were same as those of the lean principles. Lean manufacturing refers to the elimination of waste from the production system and emphasizing on those issues that add value to the products. On the other hand, the principle of FPS is to emphasize on those attributes of product that are valued and considered by the customers.
From the two definitions, it is seen that the main content is same, they said the same thing in different ways. FPS has some principles which will be amazed and compared to those of lean manufacturing technology to understand how Ford implemented lean manufacturing technology.
Production as per customer demand rather than push view:
According to Bhasin & Burcher (2006), lean production technology emphasizes on pull system which initiates the production after customer informs the company. IN Ford Production System (FPS), the company initiates the production after it receives the number of orders. Ford can do it through Synchronized Material Flow technology that produces only the required products (Attached case of Ford). As a result the company implement one of the principles of lean manufacturing technology.
Continuous improvement to reduce wastages:
Shah & Ward (2003) have revealed that one of the principles of Lean Manufacturing Technology (LMC) is to organize the workplace and arrange the process in such a way that reduces waste. FPS continuously works to improve the production system to reduce the wastage of production. This principle of LMT has significantly benefited the company to reduce wastages.
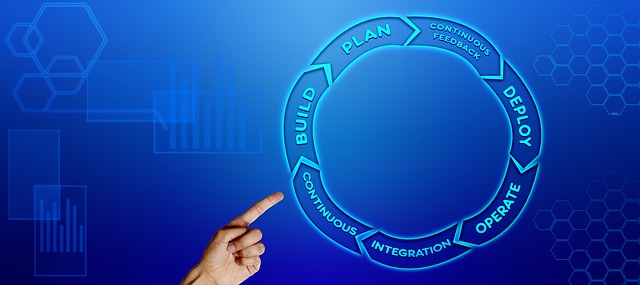
Image by Dirk Wouters from Pixabay
Just in Time (JIT) production and logistics system:
According to Hines, Holweg & Rich (2004), to reduce the level of inventory is a principle of LMT that reduces inventory. FPS reduces the level of inventory through JIT and logistics system that has direct link with the suppliers to ensure in time supply. This has established a good relation with the suppliers. This principle has helped Ford to implement LMT.
You might also find below blog posts interesting:
Pros and cons of Toyota Production System
Differences between Toyota and Ford production system
Engaging the higher managers:
Holweg (2007) has explained that engagement of the higher management at the production system is a significant principle of LMT. FPS arranged a “Lean Summit” only to engage its experienced employees who were reluctant to make a change in the organization. So, Ford has engaged the higher-ups in the production technology and thus implemented LMT.
Standardized manufacturing process in all plants:
Rothenberg Pil & Maxwell (2001), has revealed that LMT emphasizes on standardization of work process in all department and in all plants. Ford has made the use of FPS mandatory at all the plants around the world. Therefore, the company has stepped farther to implementing LMT.
Flexible manufacturing:
According to Mehrabi, Ulsoy & Koren (2000), LMT makes sure that the production system is flexible and can quickly responds to the customer preferences. Ford has adopted the principle of LMT through the initiation of flexible manufacturing which quickly responds to the changes of the market tastes. In this way, FPS has implemented lean manufacturing technology.
Ford total productive maintenance:
King & Lenox (2001) have revealed that LMT makes sure that a team always works to make the production system more efficient and profitable. This principle of LMT has been implemented by the work groups of Ford which termed the work group “Change Agents”. Thus Ford has implemented LMT in its FPS.
Application of CAD & CAM:
Kleindorfer, Singhal & Wassenhove (2005) have revealed that LMT oversees the production system, waste management before production begins to reduce the flaws in the production system. FPS also does the same job through the application of CAD and CAM that makes the visualization of the production system.
Although Ford has been able to implement some of the principles of Lean Manufacturing technology, the company has failed to adopt some principles of LMT such as “quality at source”, “Takt time” etc. If Ford adopts the complete principles of LMT, then the FPS would be more efficient.
Pingback: Operations Management of Ford - George Business Review
Pingback: Differences between Toyota and Ford production system - George Business Review
Pingback: Pros and cons of Toyota Production System - George Business Review