Contents in this Page
Executive Summary
Operations management deals with transfer of inputs to outputs in an efficient manner. Ford is a global automobile manufacturing company. This report analyses the operations management of Ford. The report found that it has some internal and external customers who are perceived very significantly by the company. The report also found that speed, cost, quality, dependability are important element in the operations management.
The production system of Ford is very much flexible and it takes much less time to market a new product. Ford emphasized much on quality, flexibility and speed of production in its business and thus it can deliver a new product quicker than its competitors can. It was recommended that Ford should focus more on cost reduction and it should introduce the universal training program for all the workers so that everyone is capable to trace any mistake in the production process.
Introduction
Operations management is concerned with converting the inputs into outputs through a series of activities to reach the operations objectives. Cost, speed, quality, dependability and flexibility are very vital issues in operations management. The main objectives of operations management are to deliver the customers with quality products in a timely manner and to maintain a sustainable relation with them. To achieve such operations objectives, a company should adopt the operations management technology in such a way that can accomplish the operations objectives. In this report, a company has been selected for application, the selected company is Ford Motor Company.
Define the principal operations tasks to satisfy these criteria
Order qualifying criteria refers to having the quality and criteria that the competitors have, on the other hand, order winning criteria provides those services and products to its customers that the competitors cannot. The principal operations task of Ford is to provide those cars and automotive items that are exclusive and preferred by most of the target customers. To qualify the order, Ford must provide quality products as per the needs and demand of the customers.
You might also find below blog posts interesting:
Pros and cons of Toyota Production System
Differences between Toyota and Ford production system
Ford implemented lean manufacturing in Production System
Analyse the process strategies and procedures employed to ensure that these tasks are carried out as effectively as possible
To qualify and win the order, Ford has implemented lean manufacturing process, as a result the company focuses on waste reduction, lead time reduction, continuous quality improvement. All of these activities have helped the company to provide those products and services that are expected by the customers. Continuous quality improvement is very essential for such technological company because it will help the company to improve the quality of products, production and to reduce the cost.
Lean manufacturing technology has helped the company to make constant improvement and to reduce the lead time of marketing the product, as a result the customers are satisfied with the company. Implementation of ERP technology at the production system is considered to be another landmark for the company because Ford wants to be updated about the production status, sales status, and inventory status. These information help the company to produce the cars on the basis of sales and foretasted demand.
An introduction in which you describe your organization and what you and your department’s contribution is to the organization
Ford is an American multinational that has operations in all the continents of the world; the company was established back in 1903. The company has specialization in producing cars, the number of employees in the company is 181,000 in 2014 (Google Finance, 2013). The company sells commercial vessels, luxury cars, tractors etc. Ford had a net income of $7.15 billion in 2013 (Google Finance, 2013). Ford is the second largest American automobile manufacturer after General Motors and it has implemented lean manufacturing in its production system (Ford, 2015).
The department which is concerned in this assignment is the supply chain department which is responsible to coordinate the production management and other functional department such as marketing, finance department of Ford. This department is very much important for the company because the efficient production and management of Ford is possible when the supply chain department is efficient.
The company has operation plant all around the world, supply chain helps the company to efficiently manage the supply chain stages of the company so that total cost of production can be reduced. Supply chain function of Ford supplies the companies with the required raw materials from the cheapest sources of the world because the company has a global supply chain network. This department also contributes to the supply of finished goods to the sales outlets and to coordinate the work-in-process goods at different plants.
An accurate description of who the customers of Ford are
Customers are the most important factor for any company because c company work to satisfy its customers (Galloway, 1998). Customers are those people of factors that expect some assistance of benefits from the company. Customers may be internal to the company or external to the company. A company must be able to identify the nature of the customers because the demand of the internal customers is different from the internal customers (Lukas & Maignan, 1996). Meeting the needs of internal customers is important because smooth function of other departments is possible if the specific department is satisfied. On the other hand, external customers want to have the desired products and services at reasonable prices.
Internal customers of Ford
Internal customers are those groups and people that help to run the company and that depend on other functional department to carry out the regular functions. In Ford, the internal customers are those people and functional departments that depend of other department to carry out the activities. These are production department, sales and marketing department, operations management department, human resource management department, accounting and finance department, supply chain management department, customer relationship management department, product innovation and development department.
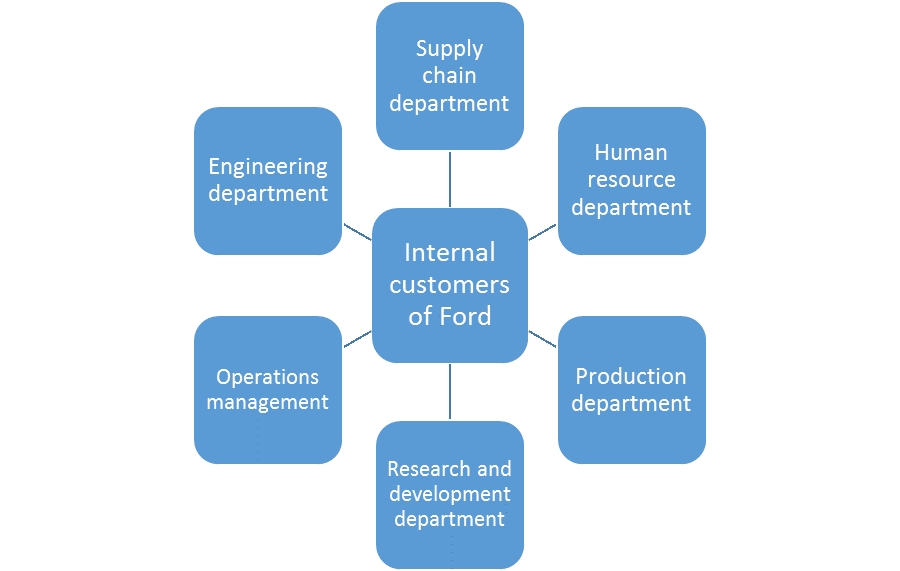
Supply chain management is a vital internal customer of Ford. It wants that sales and marketing department will properly forecast the market demand so that it can manage the supply chain efficiently. It also expects that the production department of the company will be able to deliver the required products when needed.
What are the expectations of internal customers from operations management at Ford
Production department of Ford wants that the supply chain department will assist in supplying the raw materials, sales and marketing department will assist in forecasting the production for the market depending on the market demand and finance and accounting department will help in maintaining the accounts and investment. Production department of Ford wants to produce quality products at reasonable prices.
Sales and marketing department is another important internal customer of a company. This department wants that the production department will assist it in supplying the required products and services, and the customer relationship management will help by assisting the customers after sales occur.
HR department of Ford expects that the overall image of the company will attract the talent candidates in the recruitment process so that recruiting the talent employees is possible. It also wants that existing employees be able to carry out the activities from which they are recruited to deliver the customer with excellent customer satisfaction.
Accounting and finance department of Ford want that all the functional department of the company will be able to carry out the activities as efficiently as possible so that optimal use of the resources can be possible. It also expects that all the functional department of the company will be able fully utilize the resources and reduce wastages to deliver excellent customer satisfaction.
Customer relationship management is another internal customer of Ford and it expects that the production department will be able to produce quality products and sales and marketing department can supply chain functions can properly deliver the required products to the customers to build better customer relationship. Product innovation and development is another significant internal customer of Ford and it expects that the accounting and finance department supplies enough fund to carry out the research and product development process to deliver the customer with better products and services.
Operations objectives and the processes
Performance objectives are integrally related with the operation management because it helps the company to produce the right amount at right time. The performance objectives of Ford are illustrated below:
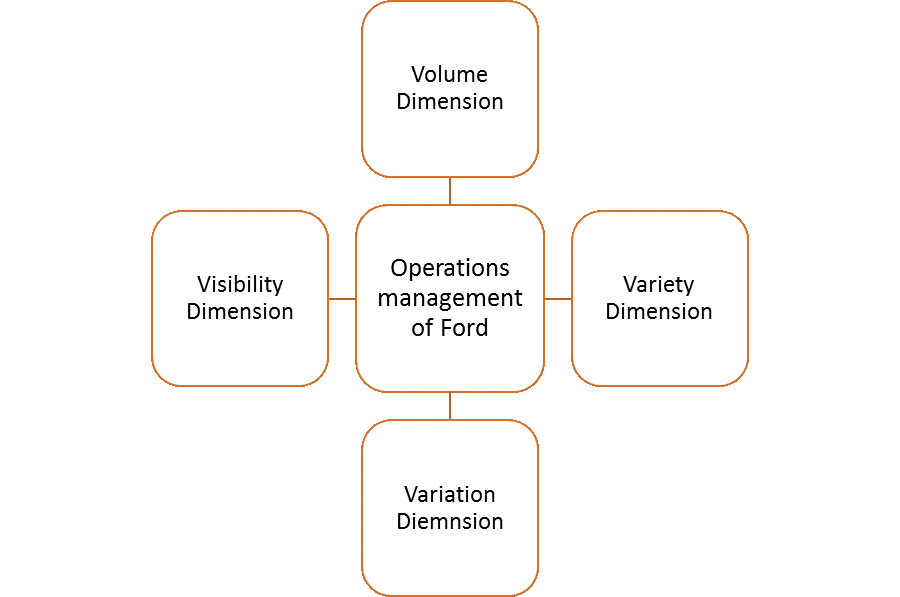
The company will produce the right amount that has been demanded by the target customers. Another important performance objective of Ford is to produce a variety of product so that it can meet a wide range of demand and preferences. The visibility dimension of the company is also very high. The company aims at make the delivery and production process visible and obvious to the target customers.
Operations of a company relates to how the activities of a company are accomplished (Stevenson & Sum, 2009). In Ford, identifying the objectives of the operations is one of the most significant fact because this helps the organization to ensure development in the operations process of the company.
Thus, in this reaction of the report, the objectives of the operations of Ford will be discussed and what process might be operating will also be analysed. Slack model is an excellent way to analyse the operation objectives of a company (Slack, 2009). In the following section, Slack model will be applied:
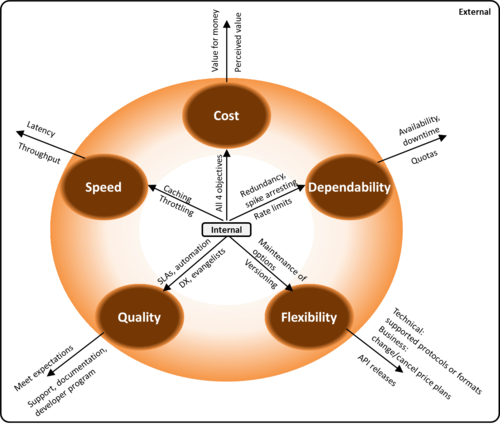
In line with the analysis of Slack, Chambers & Johnston (2009), the operations objectives of a company can be analysed on the basis of five dimensions: cost, quality, speed, flexibility, dependability. All of these factors are analysed below in relation with the operations objectives of Ford:
Cost
Cost is a major part of operations management in any company. Ford is an automobile manufacturing company and therefore, cost is a vital part of the company. The main objective of the operations of Ford should be to minimize the cost and to minimize the wastages. This can be implemented if the company optimize the manufacturing process in the plants. To minimize the cost of operations, products should be produced in the lower cost areas which have good transportation facilities to all over the world. Lean manufacturing technology should be in place to minimize the operational costs (Slack, 2005).
Speed
Speed is another important element of the operations of any company. The main objective of speed is to deliver the products in a timely manner, speeder than the competitors can. To accomplish this operational objective, there should be efficient and flawless production system, innovative sales and marketing team, excellent product innovation and development team.
Reduced new product innovation cycle
Another objective of these factors is that Ford wants to deliver the products to the customers as soon as possible just after the product is innovated. To accomplish it, there should be easy logistics system to ship the goods to the desired market.
Flexibility
Flexibility is another dimension of the operation objectives and the main concern of the operations management is that the company should be flexible in terms of production, sales and marketing and in innovation and development (Slack & Lewis, 2002). The main objectives of this dimension are that Ford will be able to change the production system whenever it wants, it will be able to adopt the technology in case of needs, it will be able to stop the production when there is any problem etc. To achieve these objectives, the company should be having lean manufacturing technology in its manufacturing system, continuous improvement and development in the manufacturing system etc.
Dependability
Dependability refers to the ability of a company to deliver the products to the customers in time (Slack Chambers & Johnston, 2009). The performance objectives of this dimension are that the company should be able to deliver products to the customers in time. To accomplish this objective, it should have in-house production system, globally scattered manufacturing plant to easily reach the customers.
Quality
Quality Quality is the most important dimension of the model (Flynn et al., 1990). Operations objective of the company is that Ford wants to deliver excellent quality product to its customers. To achieve the operational objectives, there should be continuously improvement system in the production system and all the workers of the company should be able to trace work defects so that the production can be stopped at the first sight of defects.
Process of the operations management of Ford and how process helps to achieve objectives
Ford is a world-class auto manufacturer that has implemented lean manufacturing technology in its plants. The company is a world leader in assembly line manufacturing technology. In this part, the operations process at Ford will be analysed and the application of Slack model in Radar diagram can be applied to show the relative importance of different dimensions of the elements of operations management.
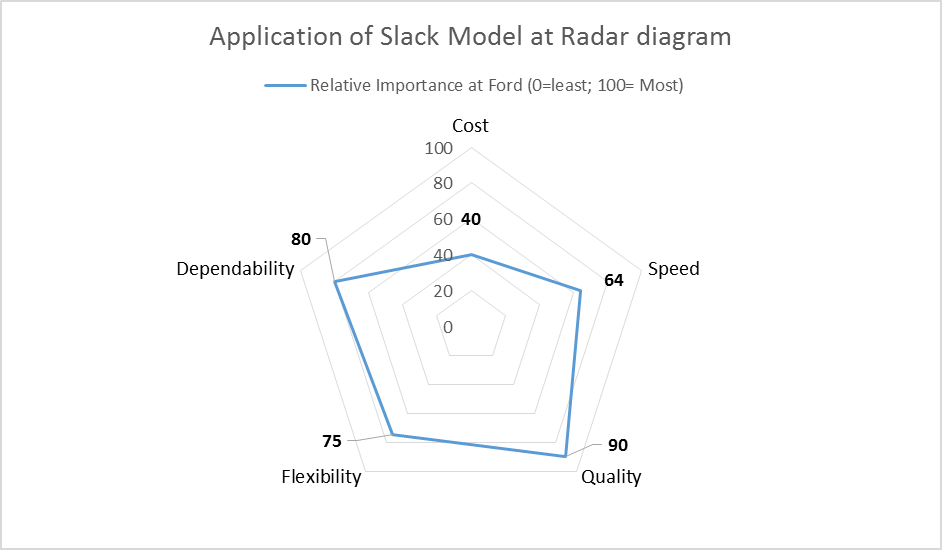
The operational process of Fords hinders cost reduction efforts
Cost is a major part of the production technology of Ford Motor Company. The main intention of the company is produce luxury cars and vehicles and thus cost reduction is a minor issue in Ford (Schaal, 2014). The company emphasizes on the relax issue of the customers and thus cost reduction is a minor issue for the company. But the operational objective of the company is to minimize the cost of production, but practically, it is seen that cost reduction is not prioritized in the manufacturing process of Ford. Therefore, the vision and manufacturing technology hinders the company to achieve the operations objectives.
Speed helps the operations management of Ford
Speed is a major issue in the manufacturing process of Ford and the company is committed to deliver the product to the customers in a timely manner. To accomplish this objectives it has a world-class innovation and development team who continuously conduct the research to develop newer products to satisfy the customers (Ford Motor Company). On the other hand, the company has more than 65 manufacturing plant all over the world that has helped the company to quickly deliver the customers with products and services (Ford Motor Company). These two types of process are very much helpful for the company to meet the objectives of delivering the customers wilt better products and services quickly than the customers can. Therefore, these processes helped to achieve the operations objectives.
Upholding quality is important for Ford
Quality management is a major issue in the Ford Motor Company because the company promises its customers to deliver quality products. To ensure quality management, it applies Six Sigma in its manufacturing technology, therefore, the quality of production at Ford has increased very significantly (Gabor, 2001).
Lean manufacturing helps
Another technology that the company implemented is the lean manufacturing technology in the production system, as a result, the company has significantly been able to reduce wastages in the production system. But the company has failed to train all of its employees to trace defects in the production system, rather it has change agents to make positive changes in the manufacturing system. The implemented technology has helped the company to ensure quality products to its customers. Therefore, the operational objectives have partially been met.
Flexibility helps
Flexibility is another important issue in the company and it ensures that the production system, sales and marketing tem and finally the research and development team are flexible enough to meet the changing demand of the customers quickly (Ford Motor Company). The company has lean manufacturing technology which can be adaptive in any case; in this sense Ford has the capability to make any changes in the production system and to meet the changing demands of the market. Therefore, the technological system of the company has enabled the company to achieve the operations objectives of the company.
Dependence on third parties hinders the operations process at Ford
Ford depends on the 3rd parties for transportation of its vehicles and the company sells its products through dealers (Penske, 2015). Moreover, it has manufacturing plant in more than 65 places around the world. The company has the capability to produce the products in time. As the transportation of the company depends on the other parties ad sales depend on dealers, delay may happen in case of delivering the products to the customers. Therefore, the logistics and selling process of the company are not efficient enough to achieve the operations objectives of dependability.
Recommendations for Ford
Some recommendations can be made for Ford Motor Company to help it reach the operations objectives of the company. The company should implement the following strategic directions to reach the strategic objectives:
- Ford has passion to make luxury cars and trucks designed to address the market of higher class people, on the other hand, cost reduction is an operation strategy of the company. Ford must emphasize on the cost reduction along with the luxury design. The company should be concerned to reduce the wastages in the manufacturing process. If the cost can be reduced, Ford will be able to reach the operation objectives.
- The company has change agents who continuously work to make positive changes in the manufacturing process. In addition to the change agents, Ford should train and empower all the workers of the company so that they can too trace any defects in the manufacturing process. This will enable to the company to reach the operations objectives of quality.
- Ford should implement central warehouse in each of the major market where the company can have economies of scale. Moreover, it should establish assembly line in each major market. This will enable the company to quickly respond to the market and to reduce the operation cost.
- Ford should recognize that 3rd party logistics support will waste time and cost more, therefore, the company should implement in-house logistics support to operate the transportation facilities inside the country.
- Ford should regularly conduct training and development program for its employees so that they can be kept updated with the recent development about production technology.
- Ford should emphasize on the needs and demand of the customers and the potential stakeholders so that it can meet their expectations.
Guidance for feasibility:
The above strategic direction can be implemented by the company. To implement the cost reduction strategy, it needs to have the passion to do so. This will enable the company to reduce the cost of operations. To ensure that employees of Ford can trace the defects, it needs to train the employees. Giving the employees training may need some resources but this will save extensively for the company. The company can establish the central warehouse in the countries so that it can quickly responds to the demand of the customers.
Conclusion:
Operations management is one of the vital issues in any company. Operations management of Ford helps the company to efficiently manage the resources and activities of a company to reach the operational objectives of a company. Ford is a US car producer that sells luxury all around the world. The company emphasized on quality and speed of delivery of the products. To achieve the operations objectives, Ford should adopt the following strategic directions:
- It should focus on cost reductions.
- Ford should develop assembly line in all the major market.
- It should train the workers to trace defects in the manufacturing process.
- It should have self-transportation system in a specific country.
References:
Duffy, D. L. (2003). Internal and external factors which affect customer loyalty.Journal of consumer marketing, 20(5), 480-485.
Kleindorfer, P. R., Singhal, K., & Wassenhove, L. N. (2005). Sustainable operations management. Production and operations management, 14(4), 482-492.
Krajewski, L. J., Ritzman, L. P., & Malhotra, M. K. (2012). Operations management. Pearson Education Limited.
Lukas, B. A., & Maignan, I. (1996). Striving for quality: the key role of internal and external customers. Journal of Market-Focused Management, 1(2), 175-187.
Stevenson, W. J., & Sum, C. C. (2009). Operations management (Vol. 8). Boston, MA: McGraw-Hill/Irwin.
Slack, N., Chambers, S., & Johnston, R. (2009). Operations management. Pearson Education.
Slack, N. (2009). Operations and process management: principles and practice for strategic impact. Pearson Education.
Slack, N. (2005). The changing nature of operations flexibility. International Journal of Operations & Production Management, 25(12), 1201-1210.
Slack, N., & Lewis, M. (2002). Operations strategy. Pearson Education.
Pingback: Differences between Toyota and Ford production system - George Business Review
Pingback: Ford implemented lean manufacturing in Production System - George Business Review
Pingback: Pros and cons of Toyota Production System - George Business Review
Pingback: How to manage a Project - George Business Review